Cart
Your shopping cart is empty! What is grease fittings?
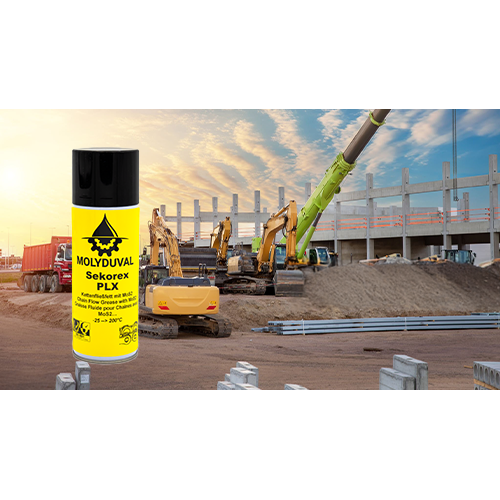
Times Read: 157 Comments: 0
GREASE FITTINGS
Specific applications with grease fittings depend on the type of machinery, operating conditions, and environmental factors. Here’s a tailored guide for various scenarios:
Heavy-Duty Construction Equipment (Excavators, Loaders, Bulldozers)
- Challenges: High loads, exposure to dirt, mud, and water.
- Fitting Recommendations:
- Use button-head fittings for high-pressure lubrication points such as joints and pins.
- Install stainless steel or corrosion-resistant fittings in exposed areas.
- Additional Advice:
- Grease daily or according to the manufacturer’s schedule to prevent premature wear.
- Clean fittings with a rag or brush before applying grease to avoid contaminant injection.
Automotive Applications (Cars, Trucks, Tractors)
- Challenges: Frequent movement, road debris, and variable temperatures.
- Fitting Recommendations:
- Use standard straight fittings for accessible areas.
- Use angled fittings for hard-to-reach suspension points or driveshaft U-joints.
- Additional Advice:
- Inspect fittings during oil changes to ensure they’re not clogged or loose.
- Use high-temperature grease for parts exposed to heat (e.g., wheel bearings).
Industrial Machinery (Pumps, Conveyors, Presses)
- Challenges: High operating hours, potential for over-lubrication.
- Fitting Recommendations:
- Use pressure-relief fittings to avoid over-pressurizing bearings or seals.
- Install flush fittings in areas where space constraints or moving parts might damage protruding fittings.
- Additional Advice:
- Create a lubrication schedule based on operating hours and load intensity.
- Use automated grease systems with fittings for continuous lubrication.
Agricultural Equipment (Harvesters, Plows, Sprayers)
- Challenges: Exposure to moisture, fertilizers, and field debris.
- Fitting Recommendations:
- Use sealed grease fittings or add protective caps to prevent contamination.
- Install fittings compatible with multi-purpose grease for convenience.
- Additional Advice:
- Lubricate after washing equipment to prevent rust.
- Use water-resistant grease for parts exposed to moisture (e.g., wheel hubs).
Marine Applications (Boats, Docks, Offshore Equipment)
- Challenges: Corrosive saltwater environment.
- Fitting Recommendations:
- Use stainless steel or brass fittings to resist corrosion.
- Install angled fittings for easier access in confined engine compartments.
- Additional Advice:
- Use marine-grade grease that resists water washout and salt exposure.
- Regularly inspect fittings for corrosion or clogs caused by salt deposits.
High-Temperature Applications (Furnaces, Kilns, High-Speed Bearings)
- Challenges: Extreme heat and potential grease breakdown.
- Fitting Recommendations:
- Use fittings made of heat-resistant materials (e.g., stainless steel).
- Use standard fittings combined with high-temperature grease.
- Additional Advice:
- Lubricate more frequently in high-temperature environments to prevent grease oxidation.
- Choose synthetic grease for better performance at high temperatures.
High-Vibration Applications (Mining, Railways, Heavy Transport)
- Challenges: Frequent movement causing fittings to loosen.
- Fitting Recommendations:
- Use locking couplers and vibration-resistant fittings (e.g., drive-type fittings).
- Additional Advice:
- Inspect fittings regularly for loosening due to vibration.
- Use thread-locking compounds for threaded fittings in critical areas.
Small or Precision Equipment (Robotics, Medical Devices)
- Challenges: Tight tolerances and precise grease application.
- Fitting Recommendations:
- Use needle-point couplers with flush fittings for precise lubrication.
- Additional Advice:
- Use grease with the appropriate viscosity to avoid excess resistance in small components.
- Apply only the recommended grease volume to prevent contamination.
General Best Practices for All Applications
- Standardize Fittings: If possible, standardize fitting types across machinery to simplify maintenance.
- Use Protective Covers: Install caps on all grease fittings to prevent contamination when not in use.
- Keep a Grease Chart: Document lubrication points, grease types, and schedules for efficient maintenance.
- Train Personnel: Ensure operators and maintenance staff are trained to recognize fitting types and avoid over-greasing.